MACHINING AND METAL FORMATION
Precision Machining Excellence
E-BI’s machining and metal formation team has a wealth of experience working with many different types of materials such as aluminum alloys, steel and plastics, in addition to countless hours of completing designs for our customers.
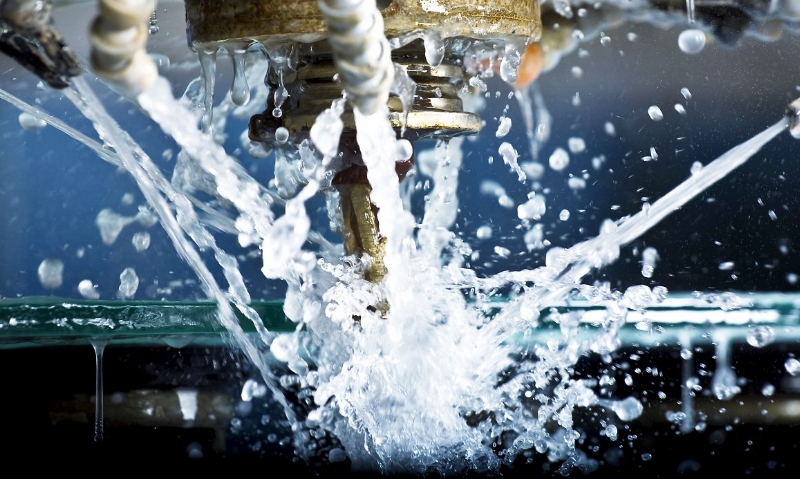
E-BI’s Machining Expertise
Metal machining is the process of taking a larger piece of metal and removing material until a desired shape and size is reached. The machining process achieves accurate dimensional results and is typically used on parts from other metal forming processes that require strict tolerances.
The 3 main machining processes are: turning, milling, and drilling. Other processes include cutting—used in a verity of applications and stages of completion—as well as grinding/polishing, done post machining to achieve a specific type of finish.
Turning
Performed on a lathe, a workpiece is spun on an axis while a blade tool removes material from the workpiece at the desired locations. The blade works along the other two axis to create precise features. This process can be automated (CNC) or performed manually.
Milling
Milling machines rotate the cutting tool instead of the workpiece. This allows the workpiece to be stationary on a fixed or movable table. Milling allows the workpiece to be machined along three dimensions. Milling machines offer the most flexible form of machining as they can perform a wide verity of cuts with on small or large workpieces using a single machine. Modern automations now allow some milling machines to automatically change cutting tools.
Drilling
Drilling is used to cut cylindrical holes in workpieces. Despite its simplicity, drilling is a highly important process as it aids in assembly of the finished piece and is used to form locating features when used in tandem with other formation process. Most fiducials—0,0 origin of the part—will be produced by drilling. Drilling can be done manually or through an automated process.
Chemical Etching
Chemical etching is a process that removes material. A stencil of chemical resistance material is applied to the top and/or bottom of the surface of a metal sheet. The metal piece is dipped into a chemical bath or chemicals are sprayed onto the metal. If both sides do not have chemical resistance paper, the acid will penetrate the whole piece. If only one side of the sheet metal has the chemical resistant film, only partial of the metal will be removed. This creates very accurate clean cuts in the metal.
Cutting
Cutting involves taking a large piece of metal and breaking it into smaller pieces or parts. The end shape is typically similar to the desired end piece. Cutting is used to get stock metal closer to the desired end result in timely manner before transfer the workpiece to another machining operation for final finishing. The most common cutting machines are: saw/blade, laser/plasma, water jet, and wire EDM.
Grinding / Polishing
When parts come out of a metal formation process, they typically lack the finish or surface appearance desired. Grinding and polishing are used post process to remove access material from previous processes. A very thin top layer of material is removed off the part to achieve a smooth or textured finish.
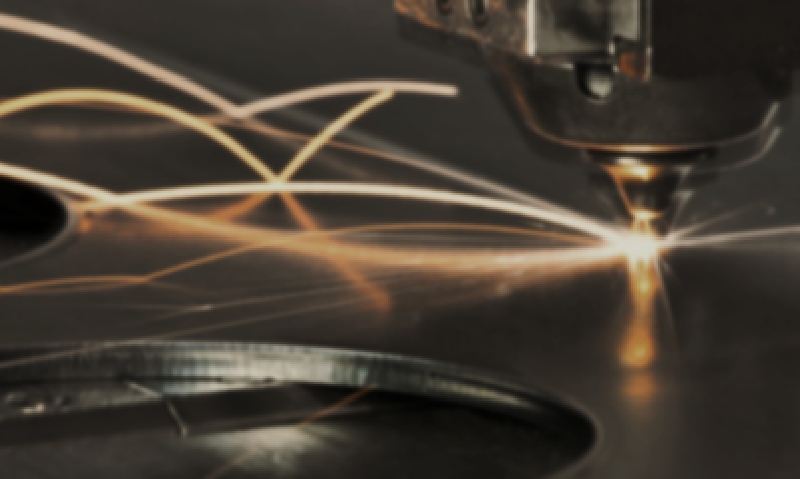
E-BI’s Metal Forming Expertise
Forging (Steel and Aluminum)
Forging starts with stock metal (rod, bar, sheet) and through rapid localized impact force, metal is formed into a desired shape. This can be done when metal is cold, warm or hot. The resultant piece of metal normally becomes stronger than the stock piece. Forging produces a stronger piece of metal than other processes, such as casting. [hot forging, temperature above re-crystallization temperature, warm, between re-crystallization temperature and 30% of re-crystallization temperature, cold below re-crystallization temperature]
Extrusion
Bar or Rod stock is forced through a die, of desired end part cross sectional shape. Starting stock piece will typically have a larger cross sectional area than of the resulting part.
Rolling
Metal stock is passed through one or more rollers (dies) to elongate (reduce thickness) the metal to the desired shape. The end result of the part will have a much more uniform thickness and cross sectional.
Stamping
Starts with sheet metal, and through sets of dies (stages), the metal is struck once per stage to deform the metal piece. The metal piece is transferred from stage to stage and through this progression, the metal is formed to the desired shape. Each stage normally performs a small amount of transformation which is why it is common to see 3-4 stages in stamping.
Bending
A stock metal sample in pressed between a lower and upper die (U shape, V shape or L shape) to deform the part to a desired angle. Typical bending operations are only preformed once, however, a series of bends can be applied to create more complex parts.
Welding
Two metal pieces of metal are melted together with a filler metal at high temperatures. The resulting weld joint will be stronger than the base metal. Because of this advantage, welding is used to join parts that would typical break from other metal processes, stamping, bending, etc.